Our Offering
The role and duties of the “Principal Designer” (PD) are critical in fulfilling and discharging the legal obligations, responsibilities and commitments set-out in the Construction (Design and Management) Regulations 2015 (CDM 2015).
The role of the PD is to:
- ensure and demonstrate that the overall design of a built structure or asset evolves in such a way that the risks associated with its entire life cycle are eliminated wherever reasonably practicable through design or, where not, are reduced As Low As Reasonably Practicable (ALARP) through the provision of effective mitigations, and;
- ensure this residual risk is clearly understood by the Principal Contractor allowing the design to be built in such a way that these mitigations are adequately and appropriately applied to ensure construction and subsequent life cycle risks are maintained ALARP.
ITPEnergised can fulfil the role of Principal Designer on your energy transition project allowing you to benefit from;
- Our knowledge and experience in fulfilling this role. We understand what’s important and how to execute it in a pragmatic way that supports and enables safe, effective project delivery.
- Our knowledge and experience in the practical and pragmatic application of the principles of ALARP, “Safe by Design” and “Hierarchy of Risk Control” – three fundamental building blocks of CDM 2015.
- Our knowledge and experience of the engineering systems, products, infrastructure etc. that comprise energy transition projects including on and offshore renewable generation, the hydrogen economy, energy storage, electrical systems and grid connection.
- Our impartiality. Being independent we are solely focussed on the safe and effective delivery of the project.
- Our collaborative team-based approach. This allows the project to benefit from our full range of knowledge and experience from right across the business rather than the specific skillset of one individual, whilst also presenting cost and efficiency savings. In addition, it allows us to support other similar projects and whilst there are obvious commercial sensitivities that we will naturally respect, this allows us to share this experience across these projects driving up standards and performance.
For more information on our wider TS&R capability, please click here.
Our Approach
Our approach is based around the following principles which we believe are fundamental to our successful execution of the PD role on any project:
Know our place
As PD, ITPEnergised do not undertake detailed design – we leave that to the suitably qualified and experienced designers appointed by the client for the different work packages. We recognise our role is to oversee each design package and coordinate all the different interfaces between these packages to ensure that the totality of the design evolves and coalesces into a final position which meets the objectives of CDM 2015.
Trust the process
In performing the PD role, we use the basic Safety Assurance Process illustrated below as a framework to guide each design package to a position which meets the three fundamental requirements of effective risk management:
- Do you know what can go wrong?
- Do you have systems in place that will stop this from happening?
- Can you ensure these systems are working effectively?
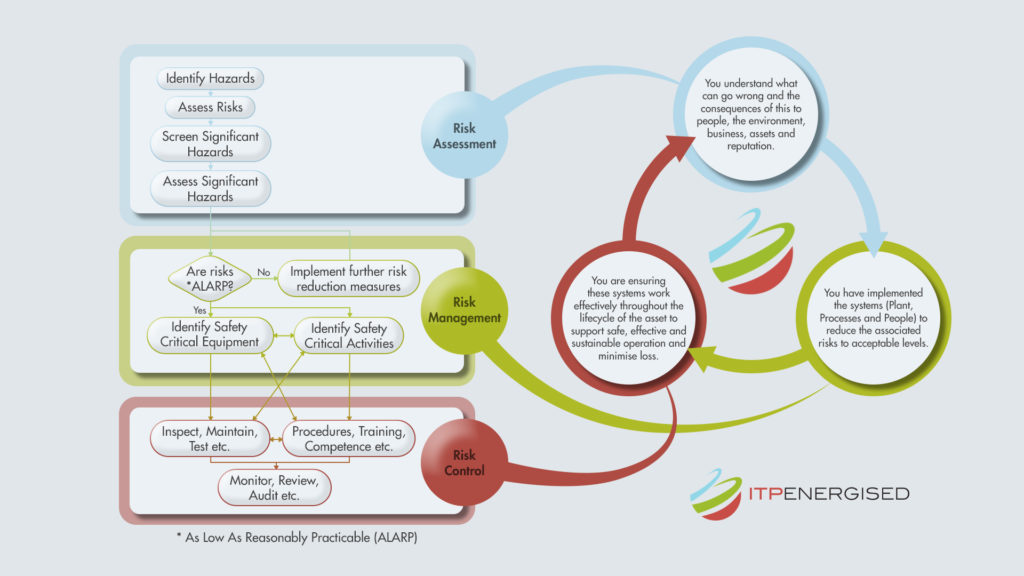
It is the responsibility of each design package owner to ensure their design evolves in a way that meets these requirements and there are lots of different ways this can be achieved. We want individual designers to adopt the best approach to suit their specific activities – that is how we can best enable project delivery. The framework above provides flexibility to accommodate different approaches and we use this to steer each design package towards the desired outcome.
Mind the gap
One of biggest risks to the successful delivery of complex, multi-disciplinary, multi-faceted projects is the failure to effectively manage the interfaces between the different design packages. Each design package owner is responsible for their package and we’ve discussed above how we provide oversight of this. If the design constraints and limitations and hazards and risks which transcend design packages are not adequately shared, then each design package will not be optimised from a health and safety perspective. Careful management of these interfaces is a key priority for us in executing the PD role.
Consider the full life cycle
A key characteristic of a typical energy transition project is that it assembles products designed and built by others into a specific configuration unique to that project. Examples of such products include a Wind Turbine, Electrical Substation or a Hydrogen Electrolyser or Fuel Cell. As a result, a significant proportion of the risk of the project is locked into the design of the product. Similarly, a significant proportion of the project risk will be locked into the logistics arrangements employed. It is therefore essential for the PD to look beyond the project risks into the product and logistics elements as illustrated below. The risks associated with the complete life cycle of the project, including product and logistics elements, must be identified as early as possible in the design process to provide the opportunity to engineer these out through design wherever reasonably practicable. This is one of the key objectives of CDM 2015 and is central to our approach in executing the PD role.
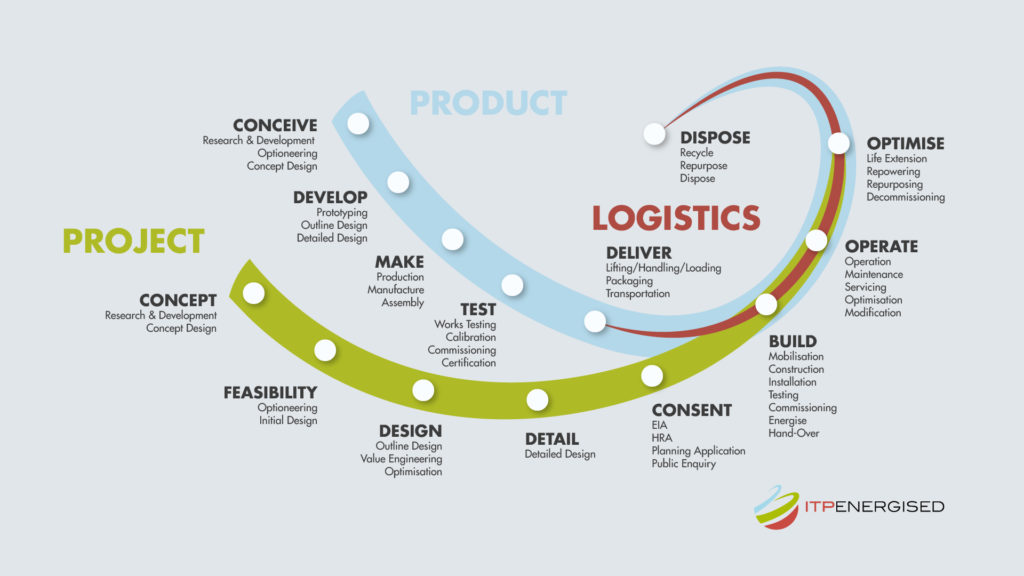
Respect the hierarchy
The principle of ALARP (As Low As Reasonably Practicable) lies at the heart of British Health and Safety – a fundamental principle enshrined within the Health and Safety at Work etc Act 1974 and CDM 2015.
Assessing whether a risk has been reduced ALARP is about weighing the risk against the sacrifice needed to further reduce it. If it is shown that the cost, time or trouble to further reduce risk is grossly disproportionate to the risk reduction benefit achieved then there is no obligation to implement these further measures. If it is shown that the cost, time or trouble to further reduce risk is less than the risk reduction benefit achieved or not grossly disproportionate, then there is a legal obligation to implement these further measures.
The principle of “gross disproportion” skews decision making in favour of taking positive steps to proactively reduce risk.
It is the responsibility of each design package owner to ensure and demonstrate their design evolves in such a way that the risks associated with its entire life cycle are eliminated wherever reasonably practicable through design or, where not, are reduced ALARP through the provision of mitigations which follow the principle of “hierarchy of risk control” illustrated below.
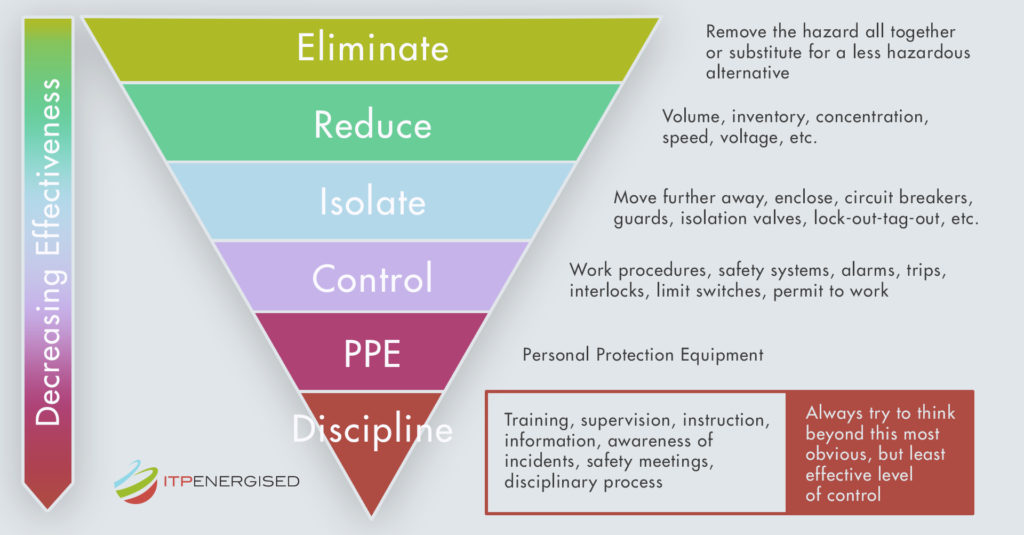
Whilst ALARP is the key principle that will drive our PD support, the “Hierarchy of Risk Control” or “ERICPD” (Eliminate, Reduce, Isolate, Control, PPE and Discipline) as it is often referred, is the framework we use to steer all facets of the design towards an ALARP position using the Safety Assurance Process previously described.
Know our onions
We believe it is essential that the PD has a sound, practical understanding of all the design elements of the project. Without this it is not possible to effectively oversee and coordinate each design package to ensure the objectives of the PD role are achieved. Given the diversity of energy transition projects, this is not possible to achieve with one individual, there are just too many different disciplines and elements to cover. That is why we adopt a team-based approach, selecting individuals expert in the different design elements and hence, collectively, are suitably qualified and experienced to oversee all facets of the complete design scope. We will not take on the PD role on any project where we cannot assemble such a team.
Safety is an enabler
Unlike more mature industries, there are no real precedents and no expansive bank of data, statistics etc. to rely on to help justify safe operations within the highly novel and innovative technologies that underpin many energy transition projects. As a young industry, we need to think creatively and innovatively to develop robust arguments as to why technologies are safe, otherwise we won’t be able to ensure safe delivery of the projects required to support the fight against climate change. We hold the strong view that safety must be a key enabler of the energy transition and this proactive, can-do attitude is fundamental to our approach.
Background to CDM 2015
The Construction (Design and Management) Regulations 2015 (CDM 2015) aim to improve health and safety in the construction industry by defining different types of duty holders with varying levels of responsibility for health and safety on a construction project.
The use of the word “construction” can be misleading on two fronts:
- It gives the perception that CDM 2015 only applies to traditional building projects such as houses, shopping centres, hospitals etc. when in fact it covers all built structures or assets and hence such diverse facilities as electrical power generation and industrial manufacturing.
- It suggests that the focus is on reducing construction risks when in fact it’s about driving designers to work together to deliver an overall asset design which protects anyone affected by the work. Designers must therefore consider the risk posed by the asset to individuals involved in its entire life cycle (construction, installation, testing or commissioning of the asset, it’s use/operation and maintenance through its design life and it’s end of life strategy, so decommissioning, disposal etc.) and either eliminate these through design or, where this is not possible, take steps to reduce or control those risks to acceptable levels.
So, rather than being limited to regulations to manage construction risk, CDM 2015 is much more far-reaching. It places a responsibility squarely on the shoulders of developers to ensure and demonstrate their assets are being designed and developed to protect people throughout its life cycle and provides a framework for them to discharge this responsibility.
CDM 2015 applies to all onshore construction projects in Great Britain. In addition, it applies to offshore renewable energy projects, specifically defined as “those harvesting energy from wind or water”, in the territorial sea and areas outside the territorial sea in the renewable energy zone defined by Section 84 of the Energy Act 2004.
Whilst certain aspects of the energy transition will fall under more stringent safety regulations such as “The Offshore Installations (Offshore Safety Directive) (Safety Case etc.) Regulations 2015” or “Control Of Major Accident Hazards Regulations 2015 (COMAH)”, CDM 2015 will be applicable to almost all energy transition projects in Great Britain.
The role and duties of the “Principal Designer” (PD) are critical in fulfilling and discharging the legal obligations, responsibilities and commitments set-out in CDM 2015.
As defined by the UK Health and Safety Executive (HSE), a PD is an organisation or individual (on smaller projects) appointed by the client to take control of the pre-construction phase of any project involving more than one design contractor. The PD has a vital role in influencing how risks to health and safety are managed throughout a project. Design decisions made during the pre-construction phase will have a significant influence in ensuring the project is delivered in a way that secures the health and safety of everyone affected by the work. The PD must:
- Plan, manage, monitor and coordinate matters relating to health and safety in the pre-construction phase. In doing so, they must take account of relevant information (such as an existing health and safety file) that might affect design work carried out both before and after the construction phase has started.
- Help and advise the client in the provision of pre-construction information and provide the information to appointed, or being considered for appointment, designers and contractors that is needed by them to carry out their duties.
- Work with any other designers on the project to identify and eliminate foreseeable significant health and safety risks to anyone affected by the work (asset/structure) and, where that is not possible, take steps to reduce or control those risks, taking into account the general principles of prevention.
- Ensure that everyone involved in the pre-construction phase communicates and cooperates, coordinating their work wherever required, including ensuring designers comply with their duties under CDM 2015.
- Liaise with the Principal Contractor (PC), sharing information relevant to the project (such as that needed for the preparation of the construction phase plan), keeping them informed of any risks and health and safety matters that need to be controlled during the construction phase; with liaison extending into the construction phase for ongoing design and gathering information for the health and safety file.
- Prepare, review and update as the project progresses, a health and safety file appropriate to the characteristics of the project, to include information that would likely be needed during any subsequent project to ensure the health and safety of anyone affected.
These requirements distil down to the two fundamental objectives of the PD role described at the start of this capability statement.
Download the CDM 2015 Principal Designer Capability Statement PDF here.
If you would like more information on how we can support you as Principal Designer on your project under CDM 2015, then please do not hesitate to contact us at info@itpenergised.com.